When Amorim Cork Composites added cork and rubber as the core material applied to sandwich wood panels (CPA - acoustic plywood) this was an innovative solution to reduce noise and vibration in interior floors for trains.
The combination of viscoelastic material (such as cork) in a sandwich panel contributes greatly to a reduction in weight and good acoustic performance.
The use of wood panels (CP - plywood and CPA - acoustic plywood) in the manufacture of indoor floors remains the dominant technology.
The new Alucork® floor, composed of a combination of a CorecorkTM core (lightweight cork agglomerate composite) with aluminum alloy skins coating each side, has taken the lead in lightweight solutions with a lower total cost available in the industry. Chart 1 shows this fact, where the Alucork® weight is substantially lower (8.6kg/m2 for Alucork® 20mm) than typical plywood and acoustic plywood solutions of comparable thicknesses.

The Alucork® floor has a total standardized thickness of 20mm (about three-quarters of an inch). This, however, is adaptable by modifying the thickness of the CorecorkTM core and, in specific cases, the thickness of the aluminum coating in order to accommodate the unique needs of each project, either in terms of structural and dimensional requirements or thermal and acoustic insulation. The final floor is a modular construction through the interconnection of the different Alucork® panels, which in turn is coupled to the carriage structure.

Aluminum alloy profiles are attached to the Alucork® panels at the time of its construction, according to the individual assessment of the needs of each project. These serve as the substrate for the mechanical coupling between panels, permitting the fastening of benches, tables, partitions, rods, technical cabinets, and others, thus guaranteeing the necessary structural reinforcement for connections with larger stresses and conferring the continuity of the surface, levelling, and the absence of visible seams on the final surface.
The incorporation of profiles in the panels is not just for the mechanical interconnection of the various panels that make up the floor and to meet fastening requirements. They are also applied to the side faces of end panels so as to ensure the peripheral sealing of the system, maximizing protection against moisture, water, lubricants, cleaning agents, and other substances foreign to the system, thereby promoting the overall durability of the system. Tests performed on this configuration attest to its effectiveness in dimensional stability and retention of the mechanical characteristics as well as the absence of fungal growth in high humidity environments.
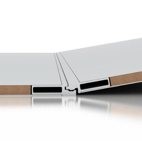
The custom and modularity design of the Alucork® panels guarantee the correct assembly and alignment of the floor as a whole, presenting a substantial improvement to efficiency in the assembly time of the final floor and respective components.